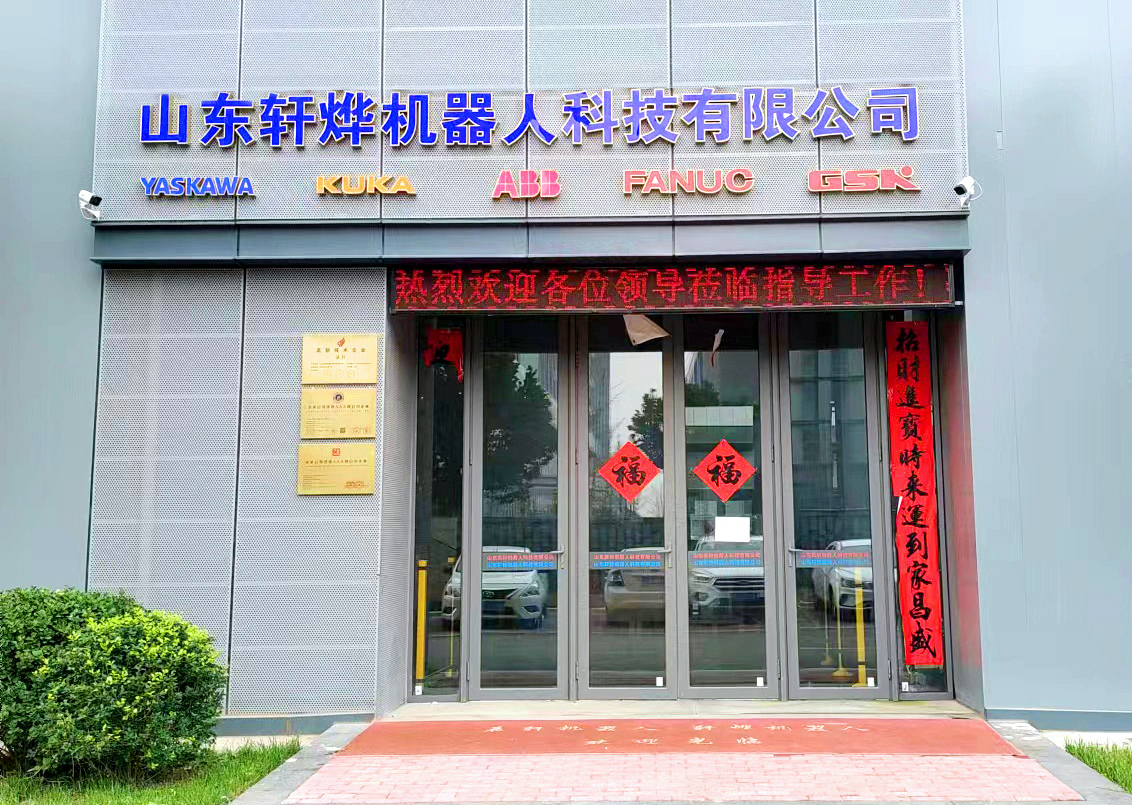
山東軒燁機器人科技有限公司是一家以工業(yè)機器人以及自動化非標設備于一體的技術企業(yè),公司致力于焊接、切割、機器人機床上下料等領域的機器人智能化研究和產業(yè)化應用
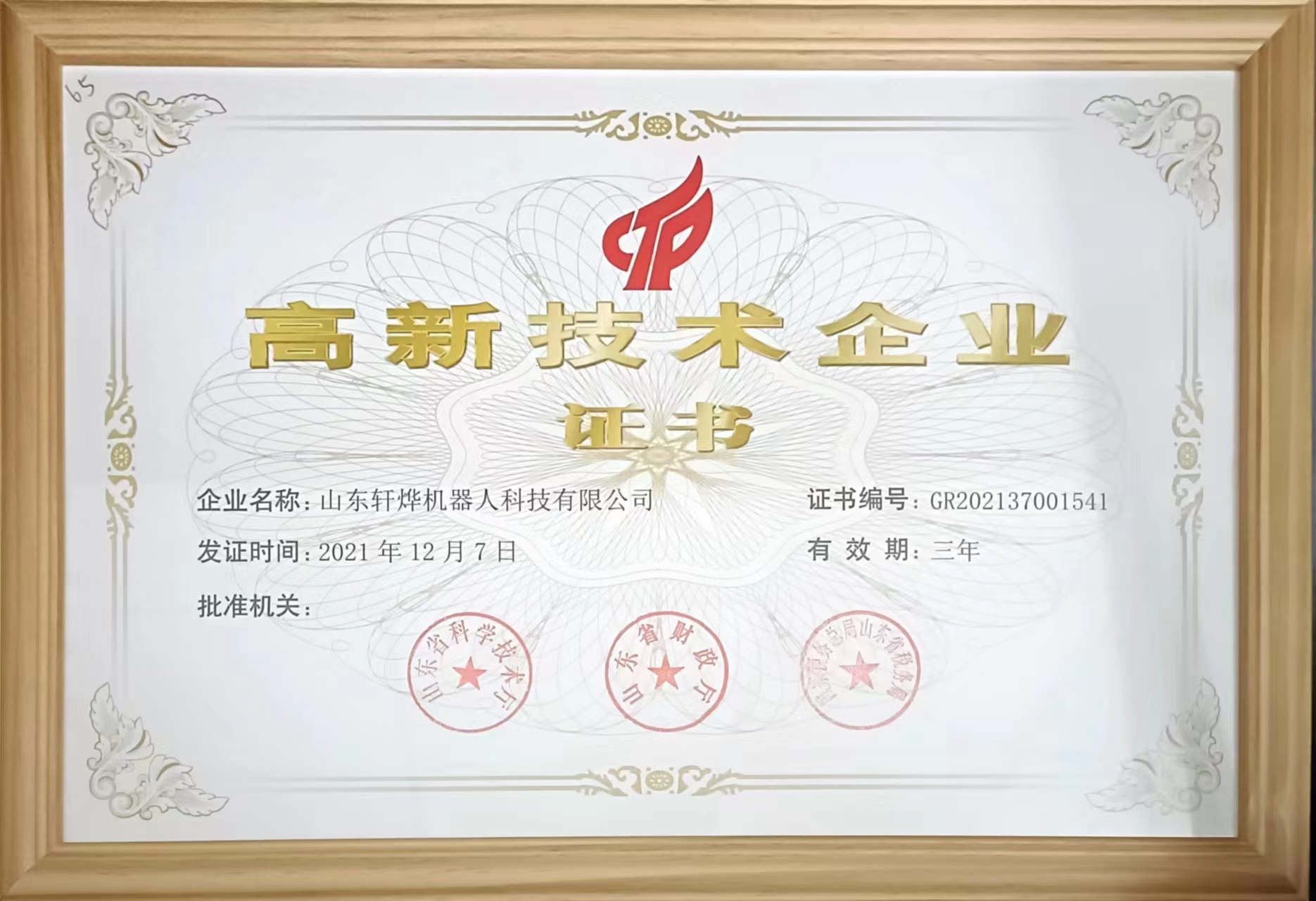
公司立足于高端裝備制造等戰(zhàn)略新興產業(yè),將追逐“制造2025"致力于機器人技術和互聯(lián)網技術的深度融合,推動智造。
發(fā)布:2024-01-22 瀏覽:0
點焊對焊接機器人的要求不是很高。因為點焊只需點位控制,于焊鉗在點與點之間的移動軌跡沒有嚴格要求,這也是機器人早只能用于點焊的原因。點焊用機器人不僅要有足夠的負載能力,而且在點與點之間移位時速度要快捷,動作要平穩(wěn),定位要準確,以減少移位的時間,提 高工作效率。點焊機器人需要有多大的負載能力,取決于所用的焊鉗形式。對于用與變壓器分離的焊鉗,30~45kg負載的機器人就足夠了。
Spot welding does not have high requirements for welding robots. Because spot welding only requires point control, there are no strict requirements for the movement trajectory of the welding tongs between points, which is also the reason why robots have long been only used for spot welding. Robots for spot welding not only need to have sufficient load capacity, but also need to move quickly between points, with smooth movements and accurate positioning to reduce displacement time and improve work efficiency. The amount of load capacity required for spot welding robots depends on the type of welding tongs used. For welding tongs separated from transformers, a robot with a load of 30-45kg is sufficient.
但是,這種焊鉗一方面由于二次電纜線長,電能損耗大,也不利于機器人將焊鉗伸入工件內部焊接;另一方面電纜線隨機器人運動而不停擺動,電纜的損壞較快。因此,目前逐漸增多采用一體式焊鉗。這種焊鉗連同變壓器質量在70kg左右。考慮到機器人要有足夠的負載能力,能以較大的加速度將焊鉗送到空間位置進行焊接,一般都選用100~150kg負載的重型機器人。為了適應連續(xù)點焊時焊鉗短距離快速移位的要求。新的重型機器人增加了可在0.3s內完成50mm位移的功能。這對電機的性能,微機的運算速度和算法都提出更高的要求。
However, on the one hand, this type of welding clamp is not conducive to the robot extending the welding clamp into the workpiece for welding due to the long secondary cable line and high electrical energy loss; On the other hand, the cables sway continuously with the movement of the robot, causing faster damage to the cables. Therefore, the use of integrated welding tongs is gradually increasing. This type of welding clamp, together with the transformer, weighs around 70kg. Considering that robots need sufficient load capacity to move welding tongs to spatial positions for welding at high acceleration, heavy-duty robots with a load of 100-150kg are generally selected. In order to meet the requirements of rapid short distance displacement of welding tongs during continuous spot welding. The new heavy-duty robot has added the function of completing 50mm displacement within 0.3 seconds. This puts higher demands on the performance of the motor, the computational speed of the microcomputer, and the algorithm.
點焊機器人的焊接裝備,由于采用了一體化焊鉗,焊接變壓器裝在焊鉗后面,所以變壓器必須盡量小型化。對于容量較小的變壓器可以用50Hz工頻交流,而對于容量較大的變壓器,已經開始采用逆變技術把50Hz工頻交流變?yōu)?00~700Hz交流,使變壓器的體積減少、減輕。變壓后可以直接用600~700Hz交流電焊接,也可以再進行二次整流,用直流電焊接。焊接參數(shù)由定時器調節(jié)。新型定時器已經微機化,因此機器人控制柜可以直接控制定時器,無需另配接口。點焊機器人的焊鉗,通常用氣動的焊鉗,氣動焊鉗兩個電極之間的開口度一般只有兩級沖程。而且電極壓力一旦調定后是不能隨意變化的。近年來出現(xiàn)一種新的電伺服點焊鉗。焊鉗的張開和閉合由伺服電機驅動,碼盤反饋,使這種焊鉗的張開度可以根據實際需要任意選定并預置。而且電極間的壓緊力也可以無級調節(jié)。這種新的電伺服點焊鉗具有如下優(yōu)點:
The welding equipment of spot welding robots adopts integrated welding tongs, and the welding transformer is installed behind the welding tongs, so the transformer must be minimized as much as possible. For transformers with smaller capacity, 50Hz power frequency AC can be used, while for transformers with larger capacity, inverter technology has been adopted to convert 50Hz power frequency AC to 600-700Hz AC, reducing and reducing the volume of the transformer. After voltage transformation, it can be directly welded with 600-700Hz AC power, or it can be further rectified and welded with DC power. The welding parameters are adjusted by a timer. The new type of timer has been computerized, so the robot control cabinet can directly control the timer without the need for additional interfaces. The welding tongs of spot welding robots usually use pneumatic welding tongs, and the opening between the two electrodes of the pneumatic welding tongs is generally only two strokes. Moreover, once the electrode pressure is set, it cannot be changed arbitrarily. In recent years, a new type of electric servo spot welding pliers has emerged. The opening and closing of the welding tongs are driven by a servo motor, and the encoder feedback allows for the opening degree of this welding tongs to be arbitrarily selected and preset according to actual needs. And the clamping force between the electrodes can also be infinitely adjusted. This new electric servo spot welding clamp has the following advantages:
1)每個焊點的焊接周期可大幅度降低,因為焊鉗的張開程度是由機器人精確控制的,機器人在點與點之間的移動過程、焊鉗就可以開始閉合;而焊完一點后,焊鉗一邊張開,機器人就可以一邊位移,不必等機器人到位后焊鉗才閉會或焊鉗完全張開后機器人再移動;
1) The welding cycle of each welding point can be significantly reduced, because the opening degree of the welding tongs is precisely controlled by the robot, and the robot's movement between points can start to close the welding tongs; After welding a little bit, the welding tongs can be opened on one side, and the robot can move on the other side. There is no need to wait for the robot to be in place before the welding tongs close or the robot can move again after the welding tongs are fully opened;
2)焊鉗張開度可以根據工件的情況任意調整,只要不發(fā)生碰撞或干涉盡可能減少張開度,以節(jié)省焊鉗開度,以節(jié)省焊鉗開合所占的時間。
2) The opening degree of the welding tongs can be adjusted according to the situation of the workpiece. As long as there is no collision or interference, the opening degree should be reduced as much as possible to save the opening degree of the welding tongs and the time required for opening and closing.
3)焊鉗閉合加壓時,不僅壓力大小可以調節(jié),而且在閉合時兩電極是輕輕閉合,減少撞擊變形和噪聲。
3) When the welding pliers are closed and pressurized, not only can the pressure be adjusted, but also the two electrodes are gently closed during closure, reducing impact deformation and noise.
本文由焊接機器人提供技術支持,更多的詳細精彩內容請點擊我們的網站http://www.tjhtzl.cn,我們將會全心全意為您提供滿意的服務。
This article is supported by welding robots. For more detailed and exciting content, please click on our website http://www.tjhtzl.cn We will wholeheartedly provide you with satisfactory service.
產品分類
新聞
截屏,微信識別二維碼